

Once you've found this value enter it in the Belt pitch field in the stepper motor calculator, or use one of the Belt presets from the drop-down. Anything beyond that is unlikely to be used in a laser.
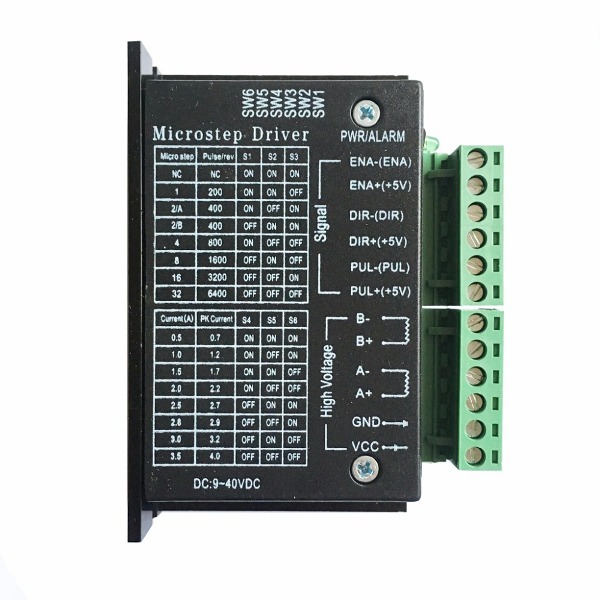
Commonly you will find 2mm, 3mm, or 5mm pitch. Just note that belts will always use nice round numbers. You can use calipers or an accurate ruler to check if you are unsure. The pitch of a belt is the distance from the center of one tooth to the center of the next. Small hobby diode lasers typically use GT2 (Sometimes called 2GT) belts which is just the name of a common belt profile that has a 2mm pitch. You will then typically be able to find specs or a datasheet on that specific motor model which will tell you the step angle. Find that and look it up online, for example: 17HS19-2004S1
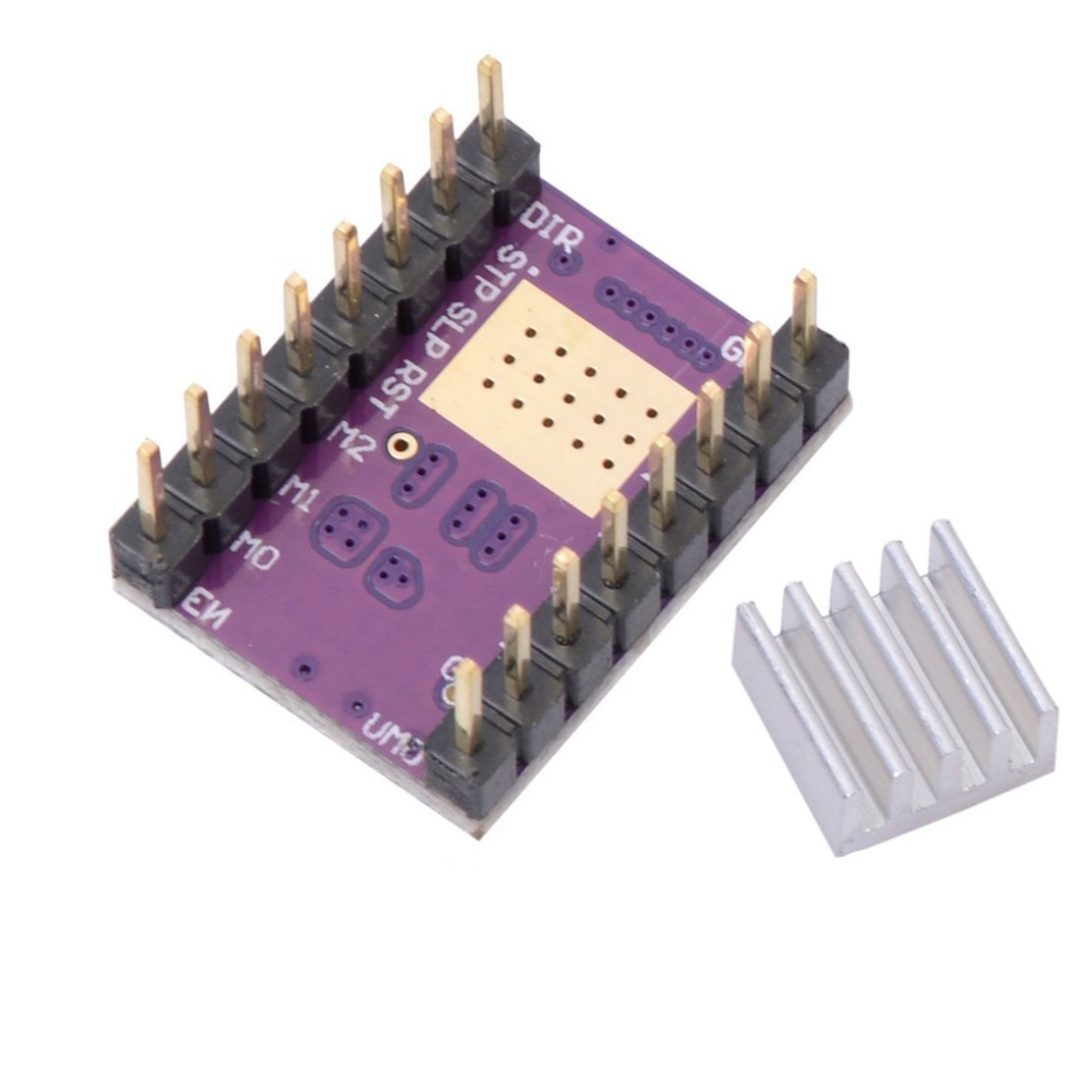
You will also likely find a model number marked somewhere on the motor. Sometimes 0.9° are used and those are very often marked as such on the motor body somewhere. It is highly unlikely the motors you are using are anything other than the 1.8° variety. We highly recommend starting by looking for the correct settings direct from the source.īarring that information being available, it can be discovered with a little work. The above is merely explaining the theory, now we need to put it all together.įirst off, the best place to find your correct steps/mm setting is generally going to be from the manufacturer of the machine (unless you built it yourself).
STEPPER MOTOR RESOLUTION CALCULATOR FULL
A common option is 1/16th microstepping which means that it divides each natural step into 16 sub-steps, multiplying the number of steps required per full rotation from 200 to 3200!Īs you can see now the steps/mm value jumped from 5 to 80 and now has a resolution of 12.5 micron or 0.0125mm.

Modern stepper motor drivers, however, can pull off a trick known as microstepping in which they can move in steps between the natural steps of the motor. That means the absolute smallest distance that can be moved is 0.2mm, which is not nearly good enough. As you can see at the bottom of the example above the resolution is 200 micron or 0.2mm. However, almost no machines will ever run in "full step" mode as shown in the example above. This is because a 20 tooth pulley represents 40mm of movement for one full rotation (20 teeth * 2mm per tooth) and there are 200 steps per full rotation. You would needs 5 steps per mm of movement. So for this configuration, as is, you would setup the calculator as shown: GT2 belts (2mm distance between each tooth)įortunately, calculating this is made easy by many great online tools, like this Stepper Motor Calculator.For small, diode-base lasers a common setup might look like: What that value is, however, depends on not just the motor but the rest of the machine's setup.
STEPPER MOTOR RESOLUTION CALCULATOR HOW TO
So in order to tell your machine how to move the correct distance it has to know how many steps to instruct each motor to move. For example, the most common motor type has a 1.8° step angle, meaning that a full rotation is 200 steps (360° / 1.8° = 200). Your laser moves by using stepper motors which, unlike basic motors, don't spin continuously but can be moved in discrete steps, each of which is a specific number of degrees in a full rotation. If you would like to better understand how the steps/mm setting works and how to actually find or calculate the true value, read on. If your movement is already close, LightBurn has a built-in Calibrate Axis tool that will allow you to easily dial in the correct setting. If what you are seeing come out of your laser looks like it's squished or stretched in one or more axis, it's very likely because your steps/mm are configured incorrectly.Īll laser cutters / engravers require that they be configured with the correct steps/mm (steps per millimeter) setting to function correctly.
